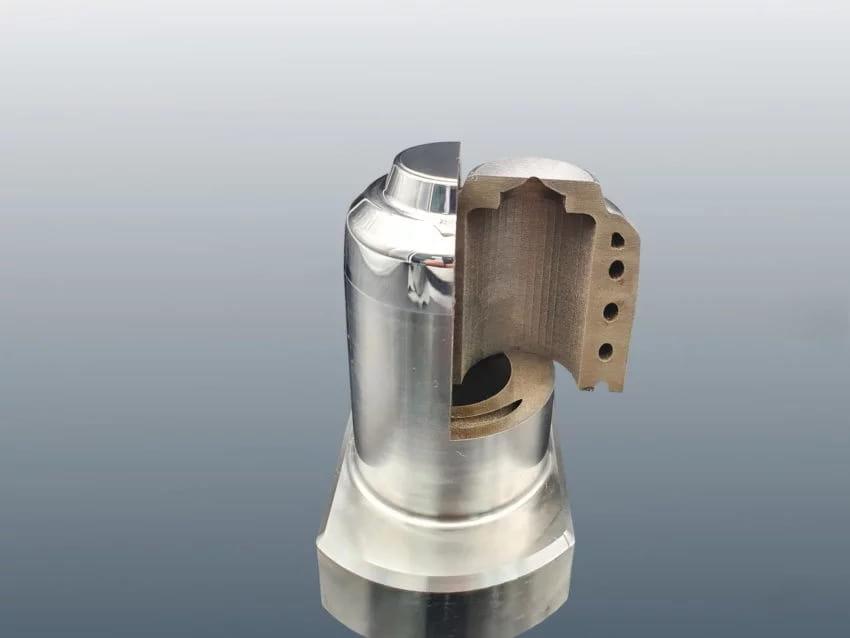
In the additive manufacturing industry, 3D printed mold inserts are transforming how companies approach injection molding. These new tools use metal 3D printing technology to improve performance and design versatility. Compared to traditional mold inserts, which can be expensive and time-consuming to manufacture, 3D printed mold inserts offer a more efficient solution. They offer various advantages, including enhanced part quality and longer lifespan, making them an appealing solution for many industries.
The advancement of metal 3D printing technology has transformed mold insert manufacturing, enabling rapid prototyping and unique designs that were previously difficult or unattainable. Whether you're working with intricate geometries or low-volume production, 3D printed mold inserts can speed up the process and provide substantial advantages over traditional approaches. In this essay, we'll go over these advantages in depth, look at real-world applications, and contemplate future advances in this intriguing sector.
What are 3D printed mold inserts?
3D printed mold inserts are advanced injection molding components made with cutting-edge metal 3D printing technology. These inserts are made by depositing material layer by layer to form the desired shape, a technique known as Selective Laser Melting (SLM) or Direct Metal Laser Sintering (DMLS). Unlike traditional machining procedures, which can necessitate extensive tooling and setup, 3D printed mold inserts provide a more adaptable and efficient solution.
The primary benefit of employing 3D printed mold inserts is their ability to accept complex geometries and unique designs. This method enables the incorporation of complex cooling channels, lattice structures, and other advanced features directly into mold inserts. These advances improve the performance of mold insert manufacture by enhancing thermal management and shortening production cycles.
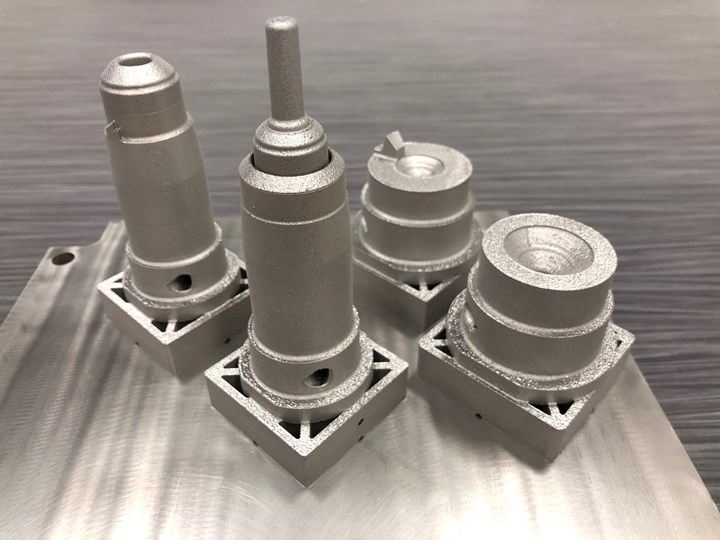
Manufacturers can swiftly iterate on designs and adapt to changing requirements with 3D printing for tool inserts, eliminating the need for costly and time-consuming retooling. This adaptability makes 3D printed mold inserts an important tool in modern injection molding, where precision and efficiency are critical.
Benefits of using 3D printed inserts
3D printed mold inserts offer a range of benefits that set them apart from traditional molding techniques.
Cost Efficiency
One of the most recognized benefits of 3D printed mold inserts is their cost-effectiveness. Traditional mold manufacturing frequently includes significant upfront costs for tooling and setup. However, 3D printed tooling inserts cut costs by eliminating the need for sophisticated and costly machining operations. This not only reduces production costs, but also makes small batches or custom parts more economically possible.
Design flexibility
3D printed mold inserts offer unequaled design freedom. Unlike traditional methods, which are limited by tooling constraints, 3D printing for tool inserts enables the production of elaborate and personalized designs. This versatility is especially useful when creating molds with complex geometries, such as integrated cooling channels or lattice systems, which improve part quality and performance.
Efficiency
3D printed mold inserts increase production speed significantly. Rapid prototyping mold inserts allow for faster mold development and customization. Manufacturers can iterate on designs quickly, test new concepts, and make changes without substantial delays, resulting in quicker overall production cycles.
Material options
Metal 3D printed mold inserts for injection molds are available in a number of materials, each with unique qualities such as strength, thermal conductivity, and corrosion resistance. This variety allows producers to choose the best material for their unique use, increasing the durability and efficiency of molds.
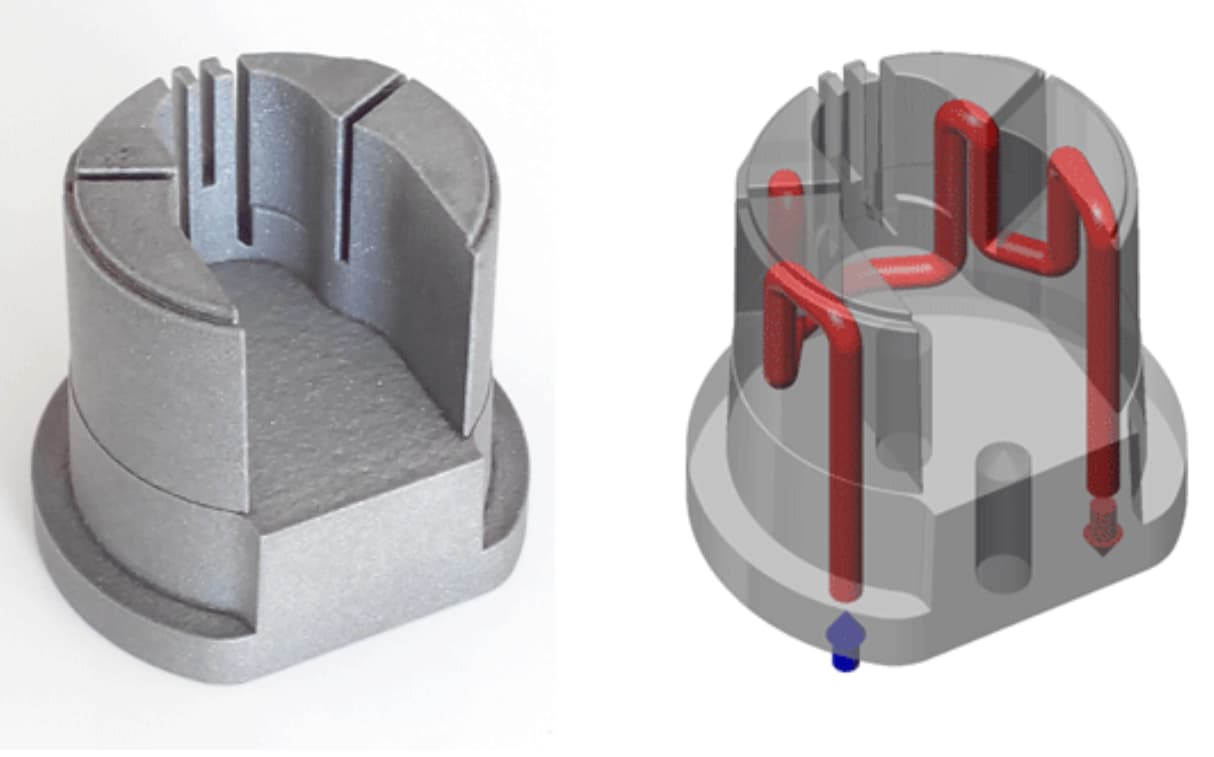
Industrial applications
3D printed mold inserts are ideal for prototype development, low-volume production, and constructing molds with intricate geometries. Their versatility and efficiency make them an invaluable asset in the plastic injection molding industry, providing solutions that previous processes cannot match.
3D printed mold inserts are revolutionizing various aspects of injection molding, offering versatile solutions across different applications.
Prototype development
3D printed mold inserts are especially beneficial during prototype development. They enable the rapid production of prototype molds that can be tested and refined quickly. This speeds up the design validation process, allowing manufacturers to test and iterate on new concepts before committing to large-scale manufacturing.
Low volume manufacturing
For projects requiring low-volume manufacturing runs, 3D printed mold parts are an effective choice. Traditional molding procedures might be prohibitively expensive for small quantities because to significant tooling costs. However, 3D printed mold inserts offer a low-cost alternative, allowing for the production of small batches without a major investment in equipment.
Complex geometries
One of the standout features of 3D printed mold inserts is their ability to handle complex geometries. Traditional molds are frequently restricted by design restrictions and tooling capabilities. In contrast, 3D printing enables the incorporation of advanced features like complicated cooling channels and elaborate interior architecture. This functionality improves the mold's overall performance as well as the quality of the finished product.
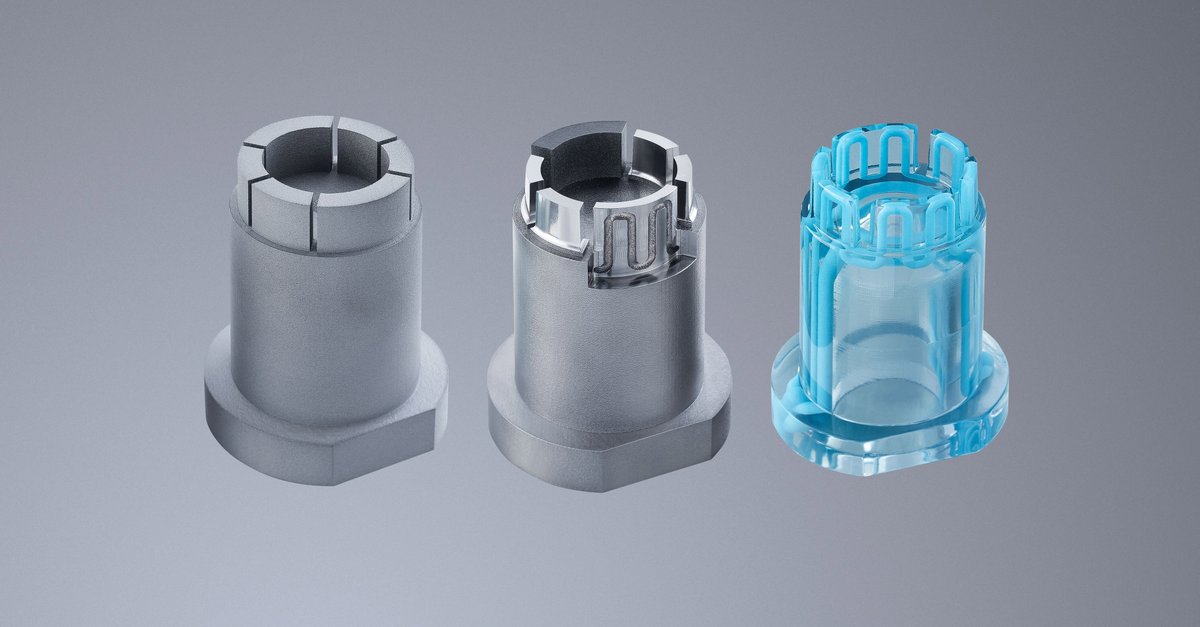
Considerations and challenges of this method
3D printed mold inserts provide tremendous benefits, but there are some issues and obstacles to address.
Material limitations
Despite advancements in metal 3D printing, these inserts' material selections may be limited when compared to traditional molds. Some 3D printed inserts may not have the mechanical or thermal properties of traditional materials; thus, it is critical to select materials that meet the molding process criteria.
Durability concerns
Although metal 3D printing has increased strength, the durability of these inserts can still be a problem, particularly under high-stress settings. To overcome this, sophisticated printing techniques and materials intended for high-performance applications are required.
Cost vs. benefit analysis
While 3D printed mold inserts can save money on some aspects, such as tooling and setup, the initial expenditure in 3D printing for tool inserts can be significant. Manufacturers must carefully consider if the benefits of 3D printing technology, such as more design freedom and shorter lead times, exceed the expenses.
Case studies and examples
Case study 1: Enhanced rapid prototyping
A major automaker used 3D printed mold inserts to expedite the prototype creation process. Historically, the company faced long lead times and expensive costs when producing new car components due to the necessity for unique tooling. They cut the time it took to create and test prototypes dramatically by using 3D printed mold inserts. The versatility of 3D printing enabled them to swiftly iterate on designs, incorporating sophisticated cooling channels and other advanced features directly into the mold inserts. This strategy sped up the design validation process while also improving the overall performance and quality of the prototype parts.
Case study 2: Low volume manufacturing for consumer goods
A consumer goods manufacturer employed 3D printed mold pieces to overcome the difficulties of low-volume production runs. The traditional method of producing pricey molds in small quantities was not cost-effective. With 3D printed mold inserts, the company was able to make high-quality molds for a fraction of the price. This allowed them to offer personalized and limited-edition goods without incurring high tooling costs. The quick turnaround time and design flexibility of 3D printed tooling inserts enabled them to respond rapidly to market demands and offer new products efficiently.
Technical trends of metal 3D printing
Thanks to developments in metal 3D printing technologies such as Selective Laser Melting (SLM) and Direct Metal Laser Sintering (DMLS), the future of 3D printed mold inserts looks bright. By enhancing strength, accuracy, and material options, these advances are expected to overcome the constraints in performance and durability that currently exist. The popularity of 3D printed mold inserts is accelerating as industries want to reduce lead times and costs due to the increased need for customizable and quick manufacturing solutions.
Conclusion
3D printed mold inserts represent a significant advancement in injection molding, offering numerous benefits that enhance both efficiency and quality. By integrating metal 3D printing technology into mold insert manufacturing, companies can achieve cost savings, design flexibility, and faster production times.
3D printed mold inserts offer significant advantages in terms of cost efficiency and design flexibility. They enable faster prototyping and more economical low-volume production, making them valuable tools in a variety of manufacturing scenarios. However, it's essential to consider material limitations and durability concerns to fully leverage the benefits of 3D printed mold inserts. By understanding these factors, manufacturers can optimize their use of 3D printing technology and enhance their production processes. At LUSHI ENGINEERING, we have more than 15 years of rich experience in injection molding and 3D printing, and are able to provide innovative solutions for modern production, improve production efficiency and save costs.