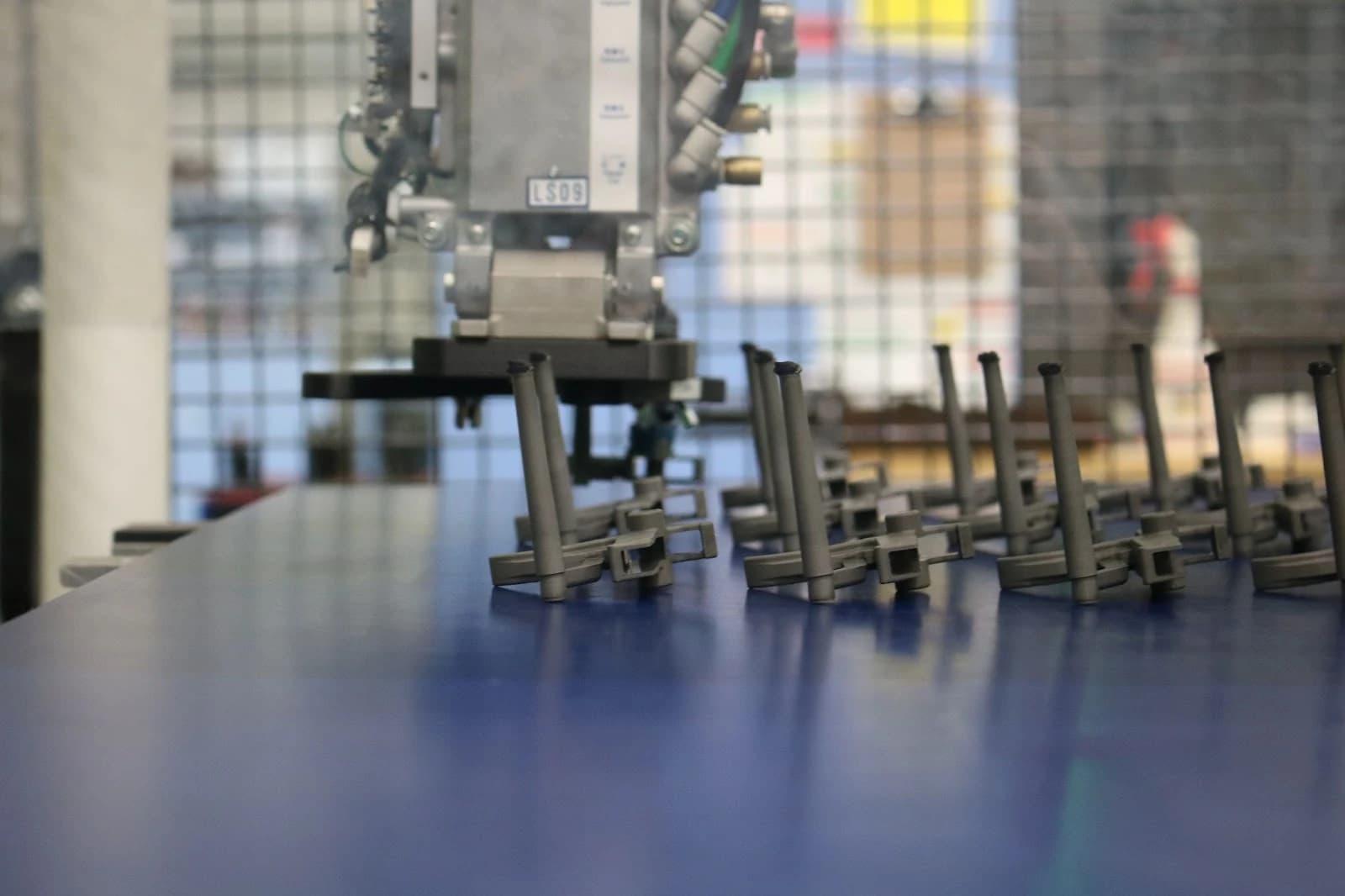
Plastics have become an indispensable part of our daily lives and various industries. Plastic forming refers to the process of creating parts, semi-finished products, films, fibers, and more using plastic materials. In the chemical industry, plastics are typically found in granules, powders, foils, or sheets. These materials are transformed into specific shapes and structures through various molding processes such as injection molding, extrusion, calendering, and blow molding. The primary forming process uses amorphous materials like powder or melt to create solid geometries, making it ideal for mass production. In this article, we will explore eight common plastic forming processes.
Plastic injection molding
Plastic injection molding process is the most widely used method for producing plastic products, accounting for 70% of all plastic production. The process begins with loading granular raw materials into a hopper, where they are heated and plasticized. The molten plastic is then injected into a mold cavity under high pressure. The parts are formed through a cooling system. This process requires molds and injection molding machines, making it suitable for mass production and cost reduction. It is compatible with various types of plastics, including thermoplastics and thermosets.
Extrusion injection molding
Extrusion molding uses an extruder system to produce continuous shapes. Raw plastic materials are fed into a barrel through a hopper, where they are melted, homogenized, and compressed. The molten plastic is then extruded through a shaped die at the end of the extruder. The shape of the die determines the product's final form. Unlike injection molding, extrusion is a continuous process. However, it is less suitable for producing complex plastic parts.
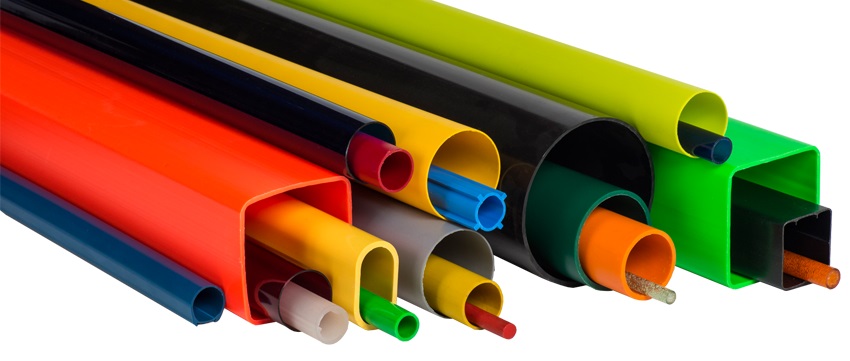
Calendering
Calendering, also known as the rolling process, is used to produce plastic films. The calender consists of several highly polished rollers that can be cooled or heated as needed. This process is especially effective for producing films with precise thickness specifications and can create embossed or patterned films.
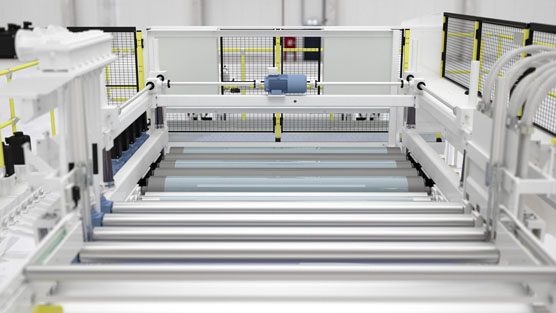
Rotomolding
Rotational molding is used to create large, hollow, and seamless plastic parts. In this process, plastic material is placed in a mold that rotates along two vertical axes and is heated. The material melts and coats the entire surface of the mold cavity, forming the desired shape. The product is then cooled and demolded. This method allows for varying wall thicknesses within a single product, making it suitable for applications such as large enclosures and containers.
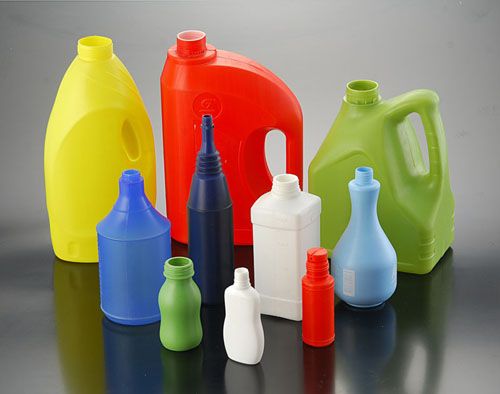
Foam molding
Foam molding produces foam by incorporating a physical or chemical foaming agent into the polymer material. This creates a honeycomb or porous structure. The basic steps of foam molding include nucleation, growth, and stabilization. The foaming process can be chemical (where a chemical foaming agent decomposes to release gas), physical (using low-boiling liquids that evaporate to form bubbles), or mechanical (stirring the plastic melt while introducing gas).
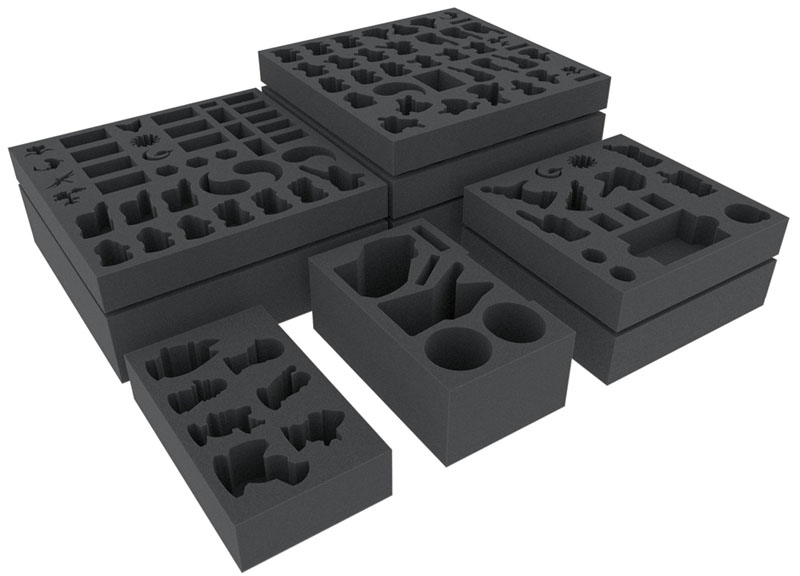
Chemical foaming process: the added chemical foaming agent is decomposed by heat to produce gas generated by the chemical reaction so that the plastic melt fills the cells—for example, the production of polyurethane foam.
Physical foaming process: First, the low-boiling liquid is added to the reaction mixture. These gases evaporate during the polymerization process, forming typical bubbles. Mechanical blowing process: Stir the plastic melt while blowing gas into the melt to form the foaming method of the cells.
Injection blow molding
Injection blow molding is used to produce hollow plastic bodies, such as bottles. The process begins by extruding a tube of plastic into a two-part mold. Compressed air is then blown into the tube, pressing it against the mold walls. Once cooled, the molded part is separated, and the hollow product is removed. This process is commonly used in the packaging industry.
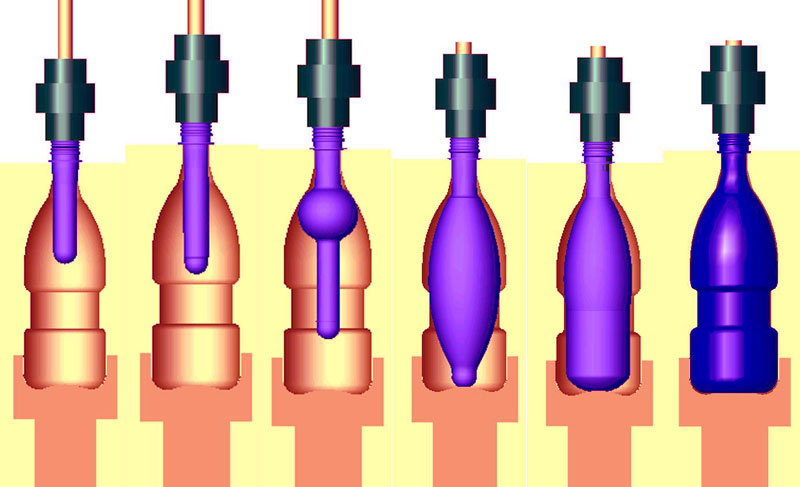
Compression molding
Compression molding involves using thermosetting plastics, which are hard and often reinforced with materials like glass fibers. The process involves placing plastic material into a heated mold, which is then closed and compressed. The heat and pressure cause the material to undergo a chemical reaction, resulting in a hardened, infusible product. This method is ideal for applications requiring high heat resistance, chemical resistance, and electrical insulation.
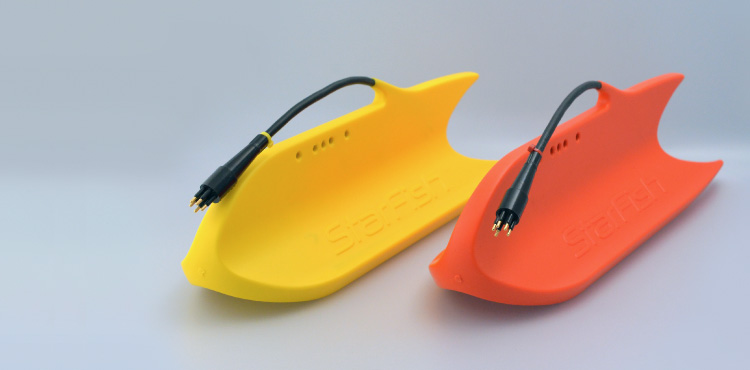
Compression molding is to add powdered or loose granular solid plastics directly to the mold, gradually soften and melt them by heating and pressing, and then shape them according to the shape of the mold cavity and solidify into plastic parts.
In the first step, powder, granular, crumb, or fibrous thermosetting plastic raw materials are directly added to the open mold charging chamber.
In the second step, the mold is heated to melt the plastic. Under the effect of the mold clamping pressure, the molten plastic fills the cavity, and then the molded part is held in this position until it hardens.
In the third part, at this time, the plastic in the cavity produces a chemical cross-linking reaction, which gradually turns the molten plastic into an infusible, hardened, and shaped plastic part. Finally, the formed plastics are removed from the mold.
Plastic vacuum casting
Plastic vacuum casting is used for thermosetting materials. In this process, liquid reactants are mixed and poured into a mold. The mixture reacts and hardens, forming the desired shape. Vacuum assistance can be used to ensure the mold is completely filled. This process is often used for prototypes and small-batch production.
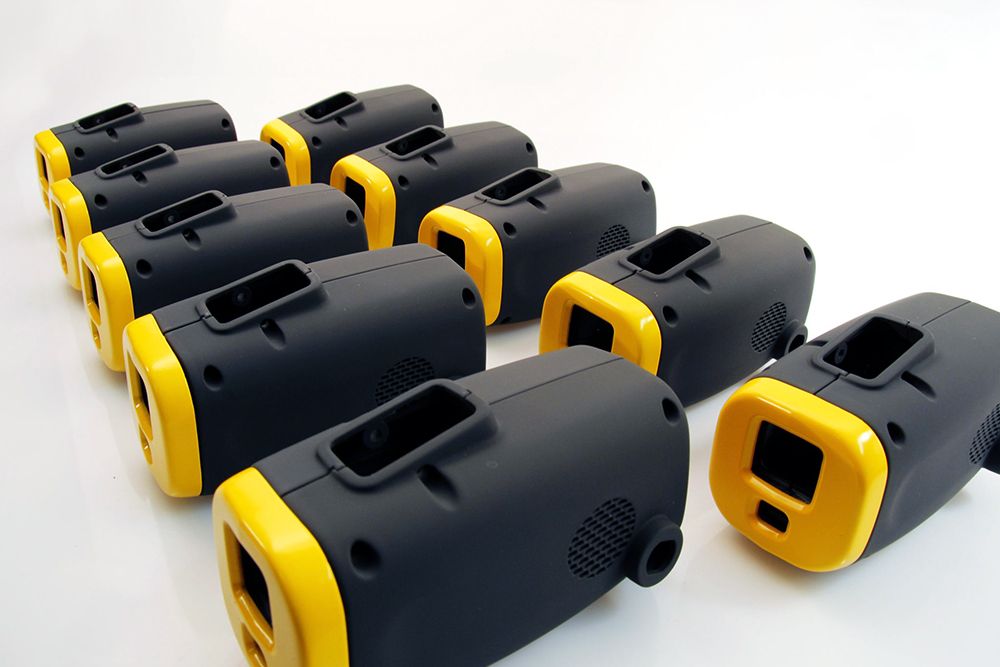
Conclusion
With over 12 years of experience in the molding industry, LUSHI ENGINEERING offers expert advice and solutions for your plastic forming needs. We ensure high-quality results while optimizing project costs. Contact us today to discuss how we can assist with your next project.