
Aluminum is a popular material for prototypes because of its remarkable mechanical qualities, which combine lightweight strength and adaptability. It is used in a variety of industries, including automotive and electronics, where long-lasting and high-quality components are required for testing and improving designs. Aluminum prototypes work well with the rapid prototyping process, enabling for the quick fabrication of scale models or functioning parts to rapidly validate design concepts.
Different aluminum prototype methods have their own set of pros and disadvantages. Choosing the appropriate technique is critical, as the wrong decision might result in considerable losses. This tutorial delves into popular aluminum alloys used in prototypes, various production processes, and their applications across industries.
Common Aluminum Alloys Used for Prototyping
Aluminum alloys are essential in the development of rapid prototypes, with each giving distinct qualities adapted to certain requirements. Each alloy's unique properties—such as strength, corrosion resistance, and machinability—are critical in determining its applicability for various aluminum prototype production techniques. Understanding these qualities assists in selecting the appropriate material for the purpose.
Aluminum 6061
It is known for its versatility and excellent mechanical qualities. It is utilized in structural applications and has excellent weldability and corrosion resistance.
Aluminum 6063
Aluminum 6063 is commonly utilized for architectural purposes due to its superior extrudability and surface polish. It is less robust than 6061, but has superior corrosion resistance and is simple to deal with.
Aluminum 7075
Aluminum 7075 is a high-strength alloy with superior fatigue resistance. It is utilized in aerospace and military applications, however it welds less well than 6061.
Aluminum 5084
Aluminum 5084 is known for its excellent strength and resistance to corrosion, particularly in maritime conditions. It is utilized in applications that demand high endurance and strength in hostile environments.
Aluminum 3003
Aluminum 3003 is a versatile alloy that may be easily formed and welded. It is utilized in applications that require moderate strength and good corrosion resistance, such as storage tanks and heat exchangers.
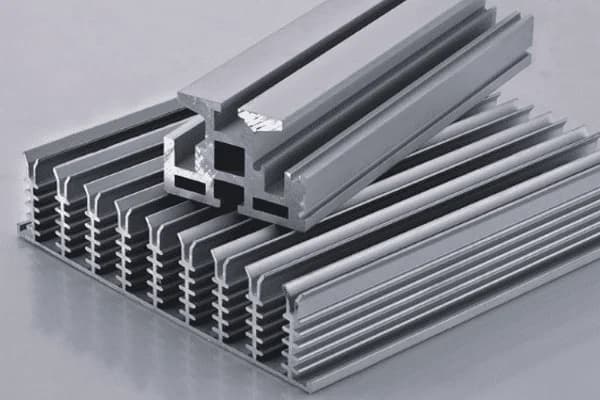
Benefits of Using Al Rapid Prototyping
Aluminum is ideal for rapid prototyping because it is lightweight, strong, and easy to machine. These benefits make aluminum an adaptable and practical material for a wide range of prototype applications, from automotive parts to consumer electronics. Its features serve to speed the prototyping process while offering consistent outcomes.
Lightweight
Aluminum prototypes provide a balance of lightweight and strength. This makes them useful for applications that require weight reduction without sacrificing structural integrity.
Cost-effective
Aluminum is typically less expensive than other metals such as titanium and steel. Aluminum prototypes are a cost-effective solution for both initial testing and manufacturing runs.
Good Thermal and Electrical Conductivity.
Aluminum's ability to conduct heat and electricity efficiently makes it ideal for prototypes that require thermal control or electrical components. This feature makes it a viable option for electronics and automotive applications.
Easy Machining and Fabrication
Aluminum's greater softness makes it easier to machine and fabricate than harder metals. This leads in shorter production periods and less tool wear, making aluminum prototypes faster and more cost-effective to manufacture.
Manufacturing Processes for Aluminum Prototypes
Aluminum prototypes are produced employing techniques such as CNC machining, extrusion, and casting. These procedures assure precision, strength, and versatility, allowing for efficient testing and development of product ideas.
CNC Machining Aluminium
CNC (Computer Numerical Control) machining is a precise way to shape aluminum prototypes. It entails utilizing computer-controlled equipment to cut and shape metal to precise proportions. This method is perfect for producing complicated geometries with high precision. Custom CNC machining is often used to create functioning prototypes with strict tolerances.
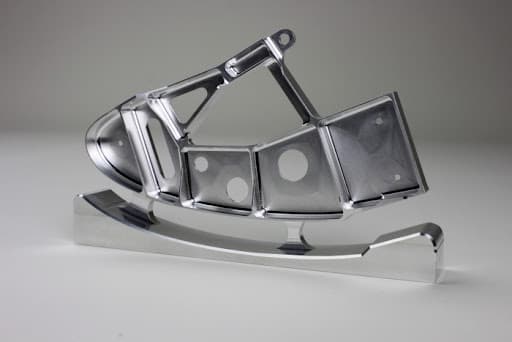
3D Printing
Aluminum 3D printing employs advanced metal additive manufacturing processes to create things layer by layer from aluminum powder. This technology enables complicated geometries and high-strength components, combining the benefits of metal 3D printing with the lightweight qualities of aluminium.
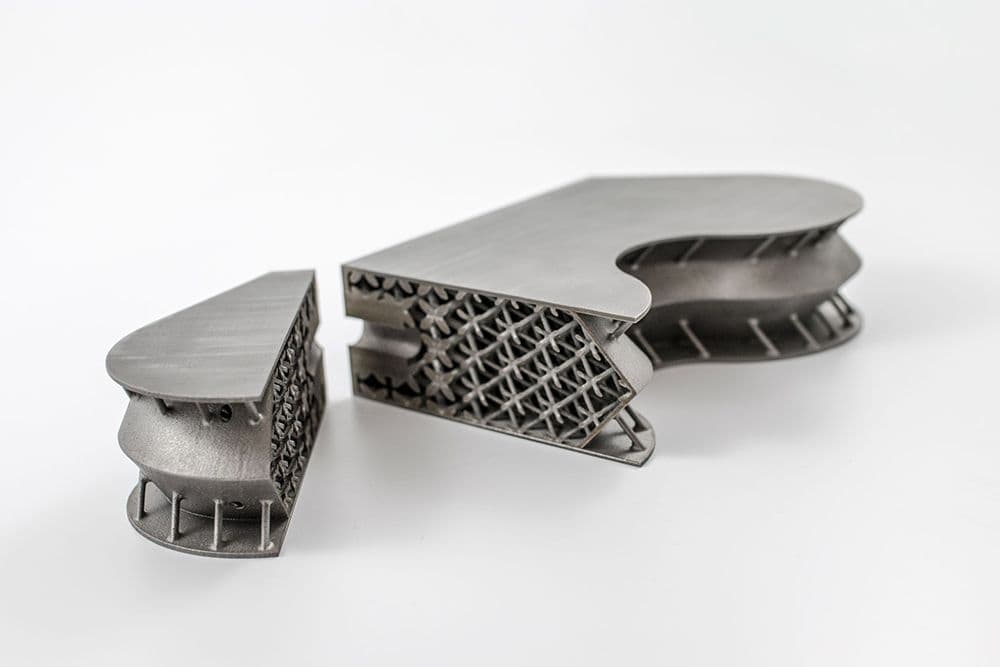
Sheet Metal Fabrication
Aluminum prototyping with sheet metal fabrication involves cutting, bending, and assembling thin aluminum sheets to create precise parts. This method offers durability and flexibility, ideal for testing designs and producing functional prototypes with a balance of strength and lightweight properties.
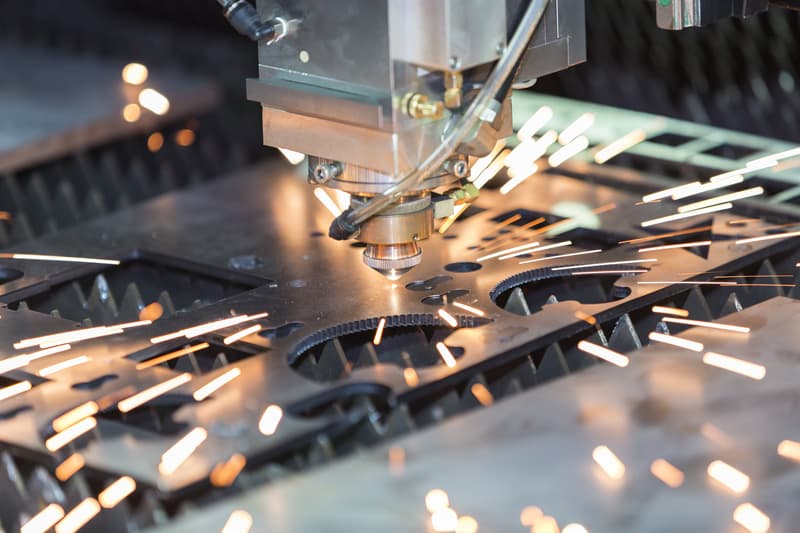
Die Casting
Die casting entails pumping molten aluminum into a mold at high pressure. This method yields prototypes with exceptional surface finish and dimensional accuracy. Die casting is suited for large-scale production and is frequently used for items that require consistent quality and detail.
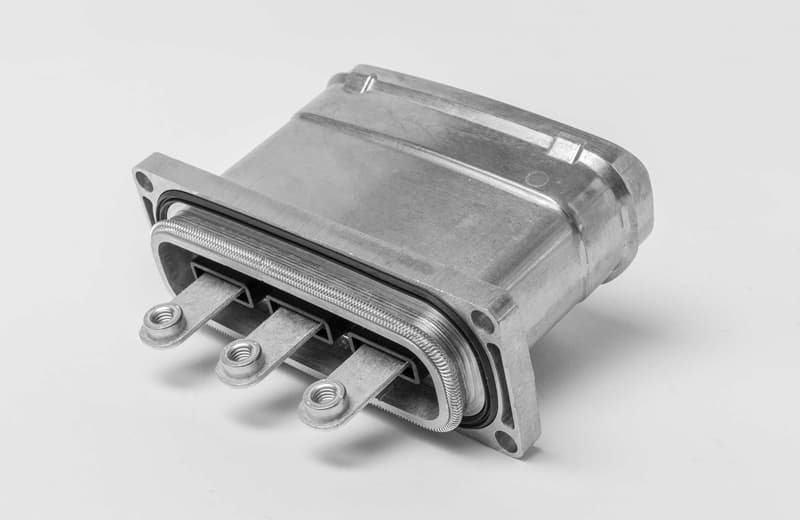
Metal Injection Molding
Although less frequent than other processes, metal injection molding can be utilized to create aluminum prototypes. This procedure entails pumping molten metal into a pre-formed mold. It is ideal for creating complex-shaped prototypes and testing design concepts in big quantities.
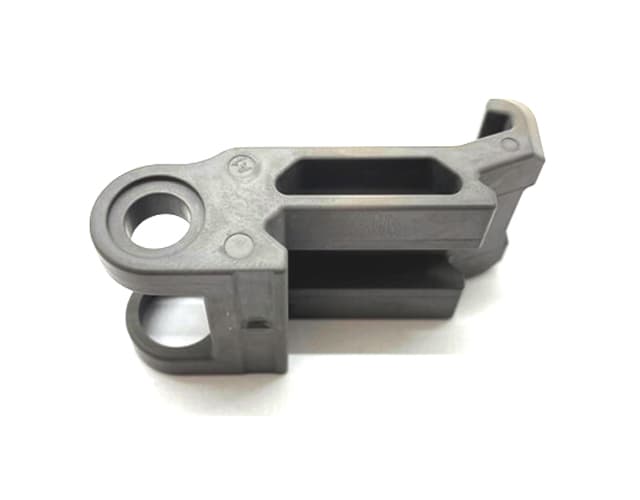
Best Practices for Aluminum Prototypes
Design aluminum prototypes with clear specifications and tolerances for accurate results. Use appropriate alloys for strength and machinability. Ensure designs account for thermal expansion and finishing processes. Regularly review and test prototypes to refine and validate functionality before final production.
Following these best practices will help ensure that aluminum prototyping perform well and meet the desired specifications, leading to successful outcomes in testing and final production.
Design Considerations
Tolerances and material qualities are important considerations while building aluminum prototyping. To avoid problems during production and use, make sure that the design parameters take into account the material's machinability and thermal expansion.
Tips to Improve Prototype Performance
To improve the performance of aluminum prototypes, optimize the design for strength and utility. Use finite element analysis (FEA) to model and fine-tune the design before manufacturing. Consider post-processing procedures such as anodizing to increase surface durability.
Common Pitfalls To Avoid
Avoid typical blunders, such as failing to consider the constraints of aluminum, which might influence prototype durability. Ensure that the design and production processes are in sync to avoid issues like warping or wrong dimensions. Additionally, ensure that the chosen production method is appropriate for the prototype's intended application and needs.
5 Considerations for Choosing the Right Method for Aluminum Prototyping
Selecting the appropriate method for aluminum prototyping requires careful consideration. Evaluating these considerations will help you choose the most suitable method for your aluminum prototyping needs, balancing factors such as complexity, volume, material properties, cost, and lead time.
1. Design Complexity
The complexity of your prototype design will influence the manufacturing process used. 3D printing may be preferred for sophisticated designs with fine details because of its ability to manage complex geometries. CNC machining is also appropriate for complex items, but may necessitate more sophisticated setup.
2. Volume Requirements
If you need to make a large number of prototypes, die casting or injection molding are more efficient. These processes are suitable for mass manufacturing and deliver constant quality, making them perfect for greater volumes.
3. Material Properties
The final prototype's material properties might be affected by various manufacturing procedures. CNC machining, for example, may produce a better surface polish and precision than die casting, which delivers greater strength and longevity. Consider the precise material qualities required for your application.
4. Cost Efficiency
Budget restrictions have a key impact in selecting the appropriate strategy. CNC machining and 3D printing are often less expensive for low-volume prototypes, but die casting and injection molding may have higher starting costs but become more cost-effective as production scales.
5. Lead Time
The time required to create prototypes varies according to method. 3D printing allows for speedy prototyping, but die casting and injection molding require longer setup times but are more efficient for larger production runs.
Industrial uses of Aluminum Prototypes
Aluminum prototypes are commonly used in aerospace, automotive, and consumer sectors to test ideas and functionality. They provide a good blend of strength, lightweight characteristics, and cost-effectiveness, making them excellent for testing concepts and refining items before mass production.
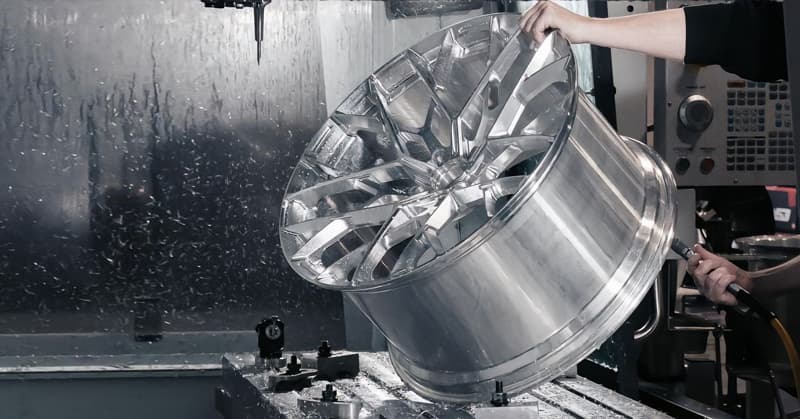
Automotive
Aluminum prototypes are used in car design to test and develop engine and structural components. They provide a lightweight option that improves vehicle performance and fuel efficiency.
Aerospace
Aerospace firms use aluminum prototypes to design components such as aircraft wings and landing gear. Aluminum's strength-to-weight ratio is vital in this industry, where weight reduction while preserving strength is required.
Consumer Electronics
Aluminum prototypes are commonly used in electronics for testing cabinets and enclosures. Their high thermal conductivity aids in heat management in electronics such as smartphones and laptops. Medical devices
Medical Devices
Aluminum prototypes are used in the medical profession to create devices and components that must be both lightweight and long-lasting, assuring dependability in important applications.
Conclusion
Aluminum prototypes combine strength, lightweight qualities, and cost-effectiveness, making them an invaluable asset in a variety of industries. Their advantages include ease of machining, high heat conductivity, and appropriateness for complex designs. Businesses can improve their product development by understanding the various manufacturing methods and best practices for aluminum prototypes. At LUSHI, we specialize in providing high-performance aluminum prototypes that are suited to your exact requirements. Our expertise guarantees that your prototypes are both functional and reliable, allowing you to meet your design objectives with efficiency and precision.