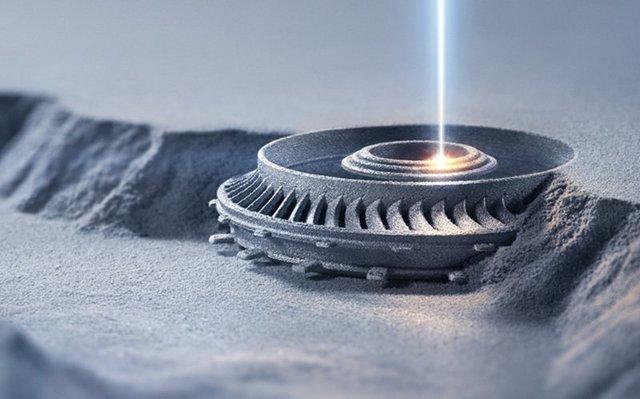
Electron Beam Melting (EBM), one of 3D printing technologies in the additive manufacturing (AM) industry, belongs to the family of powder bed fusion. Unlike Laser Powder Bed Fusion (LPBF), which employs lasers, EBM utilizes an electron beam to selectively melt metal powder within a vacuum environment, creating the desired part layer by layer. Introduced by the Swedish company Arcam in 2002, this method enables the creation of complex, highly resistant structures, and is particularly noted for its efficiency in producing components with superior mechanical properties.
EBM's ability to handle high-performance materials, including titanium, makes it especially suitable for demanding applications such as aerospace 3D printing and medical implants. The technology's adoption has been significant, especially since Arcam's acquisition by GE Additive in 2016, solidifying EBM's critical role in metal 3D printing. Today, GE Additive remains the only company marketing machines based on this process, underscoring EBM's unique position in the market and its importance in advancing high-strength, complex metal parts manufacturing.
What is Electron Beam Melting?
Electron Beam Melting (EBM) is an advanced metal 3D printing technique within the powder bed fusion, known for its precision and ability to produce high-quality metal components. This process involves directing a high-energy electron beam toward a bed of metal powder in a vacuum chamber, where it selectively melts and fuses the powder into solid layers. EBM stands out for its ability to work with high-performance metals, especially titanium, which is extensively used in aerospace and medical implants due to its strength and durability. The vacuum environment is essential in EBM, as it prevents contamination and ensures a clean melting process, making it ideal for industries that demand high-quality metal parts.
Unlike other 3D printing methods that use lasers or CO2 as an energy source, EBM relies on an electron beam, which is particularly suited for conductive metals. This unique approach sets EBM apart, as it cannot print with non-metal materials like plastics or ceramics. The electron beam's interaction with the metal powder in the vacuum chamber causes the material to solidify, creating parts with superior mechanical properties.
EBM technology has become increasingly vital in additive manufacturing, particularly in sectors requiring intricate, high-strength metal components. Its precision, efficiency, and ability to handle demanding materials make it a preferred choice in the industry.
What are the Features of EBM?
EBM 3D printing has several distinguishing qualities that distinguish it from other additive manufacturing methods. One of the most remarkable features is the ability to manufacture parts in a vacuum environment, which considerably decreases the danger of oxidation and contamination throughout the EBM process. This atmosphere is especially useful for working with reactive metals like titanium, which is widely utilized in Titanium 3D printing. Furthermore, EBM technology enables for the fabrication of parts with minimum residual stresses due to the high temperature of the powder bed during the process. Electron Beam Melting's ability to easily handle complex geometries and interior components makes it perfect for manufacturing elaborate medical implants and 3D printed turbine blades.
How Does the EBM Process Work?
The Electron Beam Melting (EBM) process starts with a computerized 3D model of the intended component. This model is divided into thin layers, with each layer's data given to the EBM machine. Metal powder is evenly spread across a build platform in a vacuum chamber. An electron cannon generates an electron beam, which is then precisely directed to selectively melt the powder according to the pattern given by the digital model. This method is done layer by layer until the entire portion is complete.
The vacuum environment in EBM is critical for maintaining the material's purity, particularly when working with reactive metals such as titanium. The high temperatures used in the EBM process aid in decreasing residual tensions, which are a typical issue with conventional metal 3D printing technologies. As the item is created, any surplus powder can be reused in subsequent builds, making the process both efficient and cost-effective.
Pros and Cons of Electron Beam Melting
Electron Beam Melting (EBM) excels in producing high-strength, precise components for aerospace and medical industries, with efficient material use and minimal oxidation. However, it has drawbacks, including high costs, rough surface finish requiring post-processing, and slower production speed compared to other methods, limiting its use in high-volume manufacturing.
Pros
High-Strength Components: EBM produces parts with excellent mechanical properties, making it ideal for critical applications in industries like aerospace and medical implants. Vacuum Environment: The EBM process occurs in a vacuum, which minimizes oxidation and contamination, ensuring high material integrity, especially when working with reactive metals like titanium. Material Efficiency: EBM allows for the recycling of unused metal powder, reducing material waste and lowering production costs. Low Residual Stress: The high temperatures involved in the EBM process reduce residual stresses in the final parts, leading to more stable and durable components. Complex Geometries: EBM can easily handle intricate designs and internal structures, making it suitable for producing complex and customized parts.
Cons
High Initial Investment: The cost of EBM machines and their maintenance is significant, which can be a barrier for smaller manufacturers. Rough Surface Finish: Parts produced by EBM often require additional post-processing to achieve a smooth surface finish, adding to the overall production time and cost. Slower Production Speed: Compared to other metal 3D printing methods like Selective Laser Melting (SLM), EBM is generally slower, which can limit its efficiency in high-volume production.
What are the Commonly Used Materials in EBM?
Electron Beam Melting is well-known for its compatibility with high-performance metals, making it a top choice for additive manufacturing in industries that require outstanding material qualities. Titanium and its alloys are the most often utilized materials in EBM 3D printing, particularly for aerospace and medical applications. Other materials include cobalt-chrome, which is widely used in dental and orthopedic applications, and nickel-based superalloys, which are suited for high-temperature conditions such as turbine blades. EBM technology's precision with these materials makes it a powerful tool for creating complex, high-strength components.
Applications of EBM and Economic Considerations
EBM is frequently employed in industries that require high component performance and dependability. EBM is used in aerospace 3D printing to create lightweight but sturdy components, such as 3D printed turbine blades. In the medical field, EBM technology is used to make customized orthopedic implants that provide a perfect fit for patients. While the initial cost of EBM machines is considerable, the long-term benefits include reduced material waste, high-quality outputs, and the ability to create complex parts with minimal post-processing. These benefits make Electron Beam Melting an affordable option for producing high-value, critical components in demanding industries.
The Strengths and Weaknesses of Electron Beam against Laser
When comparing Electron Beam Melting (EBM) with Selective Laser Melting (SLM), both methods provide distinct advantages in metal 3D printing. EBM technique excels at working with reactive metals such as titanium due to its vacuum environment, which inhibits oxidation. It also creates parts with less residual stress because to the high powder bed temperatures, making it excellent for large, high-strength components.
SLM, on the other hand, produces a finer surface polish and is often faster, making it more suited to high-volume production. However, SLM is less successful in certain materials and can introduce additional residual stress into the finished parts. The decision between EBM and SLM frequently hinges on the exact application requirements, with EBM being recommended for extremely demanding applications where material performance is critical.
Conclusion
To summarize, Electron Beam Melting (EBM) is a powerful and adaptable technique in the additive manufacturing environment, especially for generating high-strength metal components in demanding industries such as aerospace and medicine. Its ability to handle reactive metals, reduce residual stress, and operate efficiently in a vacuum environment makes it an excellent choice for applications that need precision and material integrity. However, greater costs, slower production speeds, and the necessity for additional post-processing are all factors to consider when using EBM over other methods such as laser-based technologies. Despite these shortcomings, EBM is still a vital tool for metal 3D printing producers who value quality, dependability, and creativity.