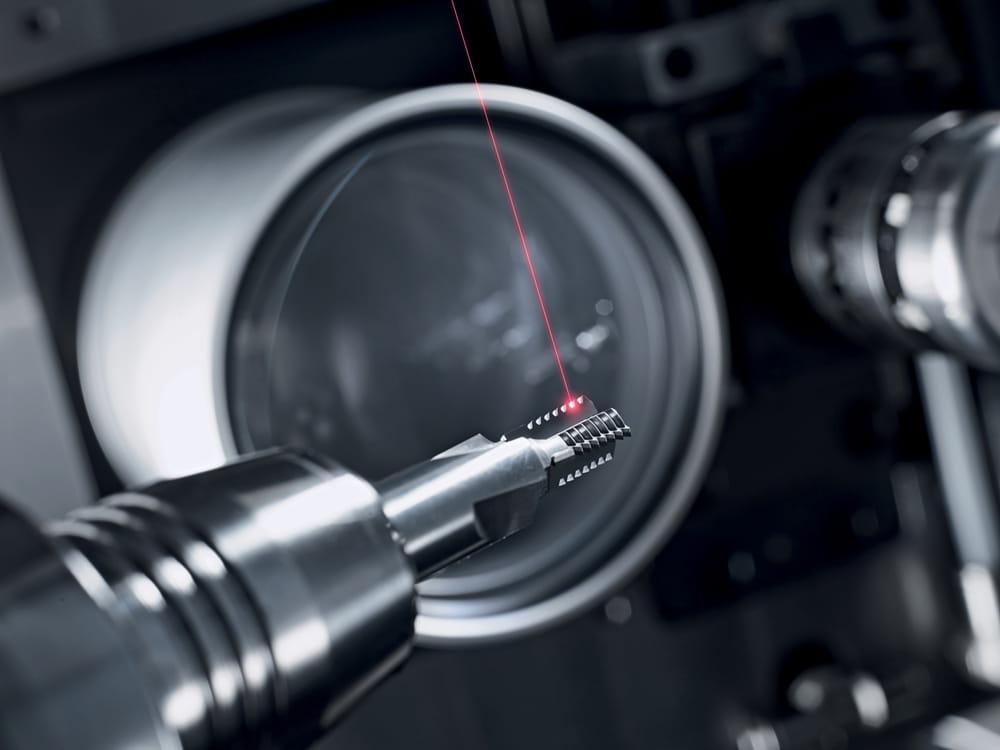
Micromachining has revolutionized precision manufacturing, particularly in the medical field. This advanced technique allows us to craft incredibly tiny and detailed components that are crucial for today's high-tech medical devices. As medical devices become more complex and precise, micromachining plays a key role in ensuring that each part meets stringent standards.
In the medical field, the importance of precision cannot be overstated. For devices like surgical instruments, implants, and diagnostic gadgets to work properly and guarantee patient safety, they must be carefully crafted. For these applications, micromachining has many advantages that range from improving precision to making it possible to produce intricate designs. This method helps to achieve improved patient outcomes in addition to enhancing the functionality of medical gadgets. As we examine the advantages and uses of micromachining in healthcare in more detail, it becomes evident how crucial a role it plays in developing medical technology.
What is Micromachining?
Micromachining is a precise manufacturing method that produces incredibly small components and features with high accuracy. This technology uses specialized equipment and processes to create components that are frequently measured in micrometers, making it perfect for applications demanding precise precision and functioning.
Micromachining employs a variety of processes, each of which is appropriate for a certain application. Micro-milling involves removing material from a workpiece with tiny cutting tools, enabling for the fabrication of complicated shapes and fine details. Micro-drilling is the process of drilling microscopic holes with precision, which is crucial for applications such as fluidic channels in microfluidic devices. Surface micromachining assembles layers of material to create detailed structures, whereas laser micromachining uses concentrated laser beams to cut or engrave precise features into diverse materials.
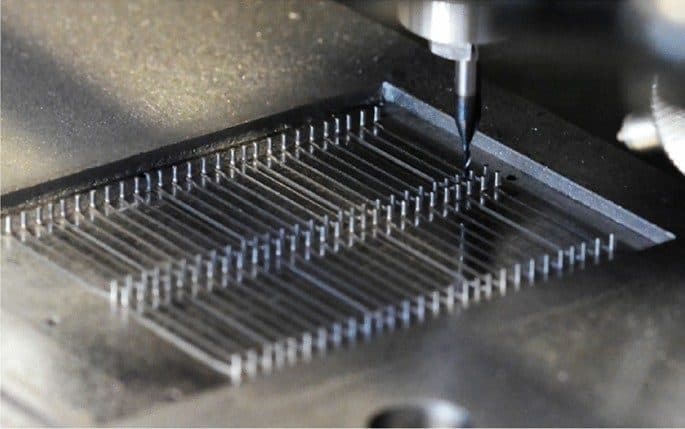
Micromachining is distinguished by its ability to attain extremely fine tolerances as well as its versatility in working with a wide range of materials. This precision is critical in industries like as medical device manufacture, where even slight errors can have a significant influence on performance. Micromachining uses these techniques to produce parts that are not only functional but also extremely reliable, making it a cornerstone technology in modern manufacturing.
Micromachining in medical component manufacturing
By enabling the creation of highly detailed and precise components, micromachining enhances the functionality and performance of medical devices and equipment, contributing to better patient outcomes and more effective diagnostic tools.
Micromachining has a transformative impact on medical component manufacture, delivering the precision required for a variety of important applications. This technology is essential for developing components that meet high quality and performance standards in the healthcare industry.
Medical device manufacturing
Micromachining is an important process in medical device manufacturing because it produces precision components for surgical instruments and implants. Surgical equipment benefit from the capacity to design sophisticated features with tight tolerances, ensuring dependability during delicate procedures. Implants such as orthopedic screws and dental implants require precise dimensions and flawless finishes, which can be achieved through micromachining.
Diagnostic equipment
The evolution of diagnostic equipment also makes use of micromachining processes. Microfluidic devices, which are used to handle small amounts of fluids in diagnostics, rely on micromachining precision to construct channels and chambers of perfect size. Similarly, lab-on-a-chip technologies combine many lab tasks onto a single chip, taking use of the precise detailing that micromachining affords.
Biotechnology & research
In biotechnology and research, micromachining makes it easier to create micromachined sensors and actuators. These components are required for precise biological process monitoring and experimentation. Custom research tools created using micromachining enable novel experimentation and breakthroughs in medical research.
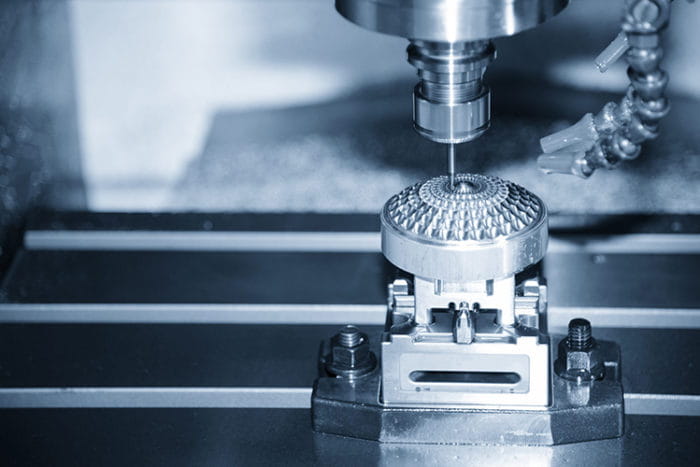
Benefits of micromachining for medical devices manufacturing
Micromachining has numerous benefits for medical applications, including improved performance and effectiveness of various medical devices and components. The precision and capability of this technology meet a number of essential needs in the healthcare business. Enhanced precision and accuracy.
Higher precision and accuracy
One of the biggest advantages of micromachining is its ability to provide higher precision and accuracy. In medical procedures, where even minor variations can have serious consequences, this accuracy guarantees that components such as surgical instruments and implants work exactly as intended. Case studies reveal that devices made with micromachining processes frequently outperform traditional approaches in terms of accuracy, which is critical for effective medical outcomes.
Improved patient outcomes
The impact of micromachining is directly related to improved patient outcomes. For example, the thorough design of micromachined implants and surgical equipment leads to improved performance and a lower risk of problems. When devices are built with high accuracy, they fit better, perform more reliably, and lower the possibility of errors during medical operations, resulting in increased patient safety and faster recovery periods.
Higher complexity
Micromachining also enables the production of extremely intricate components that would be difficult to fabricate using conventional methods. This capability permits the creation of modern medical devices and diagnostic equipment that may perform several functions or have intricate characteristics, resulting in considerable advantages in both diagnoses and therapy.
Commonly used medical grade materials
In micromachining, selecting the appropriate materials is crucial for ensuring the performance and reliability of medical components. Various medical grade materials are commonly used due to their specific properties that meet the stringent requirements of medical applications.
Stainless steel
Stainless steel is commonly utilized in micromachining due to its high strength, corrosion resistance, and biocompatibility. It is widely used in the manufacture of surgical equipment and implants, where toughness and resistance to physiological fluids are required.
Titanium
Titanium is preferred due of its great strength-to-weight ratio and high biocompatibility. It is commonly utilized in micromachined implants and prosthetics, especially in applications requiring lightweight and robust materials, such as orthopedic and dental implants.
Polymethylmethacrylate (PMMA) Polymethyl methacrylate (PMMA), generally known as acrylic, is utilized in micromachining because it is optically clear and easy to treat. It is used in devices that require clarity and precision, such as certain diagnostic equipment.
Silicone
Silicone offers flexibility and biocompatibility, making it suitable for micromachined components that need to conform to complex shapes and provide a soft touch. It is commonly used in applications like seals and gaskets in medical devices.
Bioresorbable polymers
Bioresorbable polymers are utilized in temporary implants and scaffolds that disintegrate naturally in the body. Micromachining these materials enables fine control over the deterioration rate and structural integrity of the implants.
Ceramics
Ceramics are prized for their hardness and wear resistance. Ceramics are utilized in micromachining for components that need to be long-lasting and precise, such as diagnostic equipment or implants.
Conclusion
Micromachining presents significant benefits for healthcare by enabling the creation of highly precise and intricate components, which are essential for advanced medical devices and diagnostic tools. This technology enhances surgical instrument precision and facilitates the production of sophisticated implants and microfluidic devices, contributing to better patient outcomes through reliable and effective devices.
However, micromachining in healthcare also faces several challenges. The complexity of working with tiny components necessitates specialized equipment and techniques, making consistent precision difficult to achieve and affecting quality control and production costs. Material limitations can further complicate the process, as not all materials are suitable for micromachining or may require additional processing. Additionally, the high cost of advanced equipment and the need for skilled operators can impact large-scale production feasibility.
To fully leverage micromachining's potential, ongoing advancements in technology, materials, and production processes are essential. Despite these challenges, the promise of micromachining in transforming medical technology and improving patient care is substantial. Embracing this technology can position you at the forefront of innovation in healthcare.