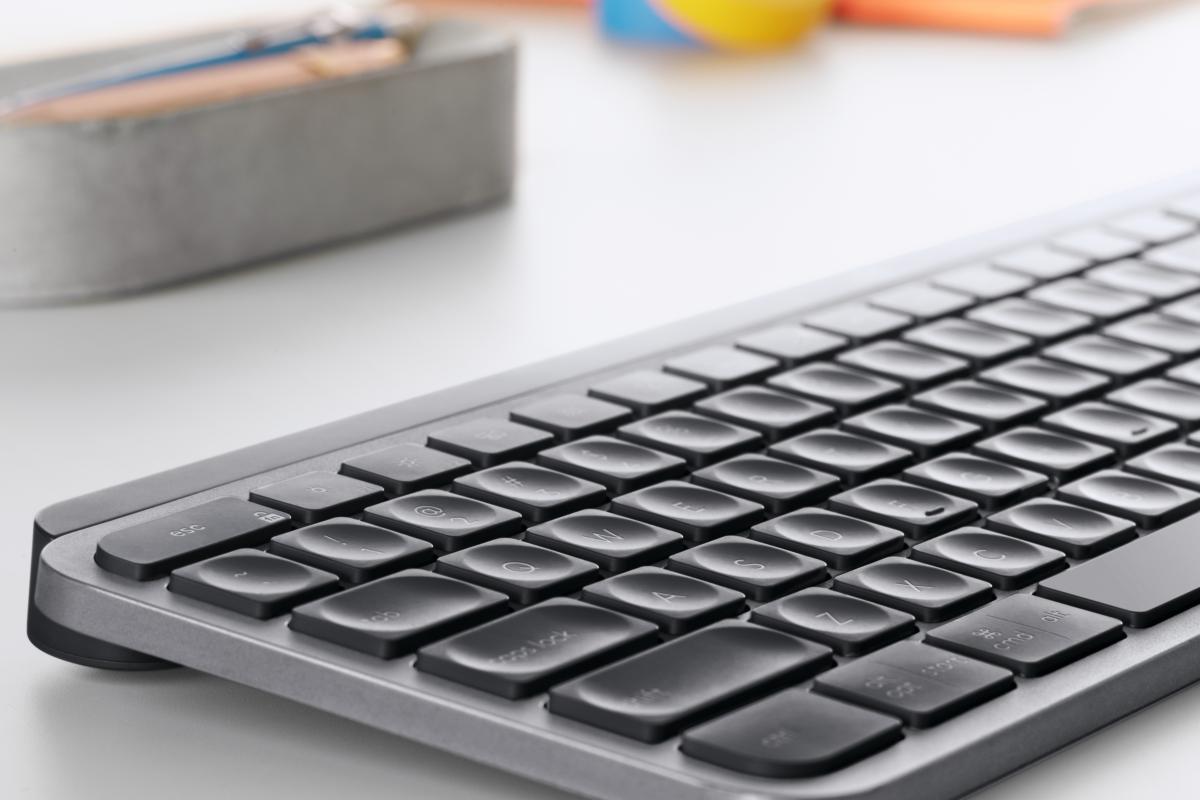
ABS, commonly known as acrylonitrile butadiene styrene, is made from the copolymerization of three monomers: acrylonitrile, butadiene, and styrene. Therefore, the ABS resin material has the common properties of the three components. In the ABS structure, acrylonitrile makes it resistant to corrosion, heat-resistant, and has good surface hardness; butadiene makes it highly elastic and tough; and styrene has good thermoplastic processing properties. ABS plastic resin is easy to get from the raw materials, has superior overall performance (toughness, hardness, and rigidity), is low on the market, and has a wide range of uses. Besides, it is also the most commonly used plastic material in injection molding manufacturing.
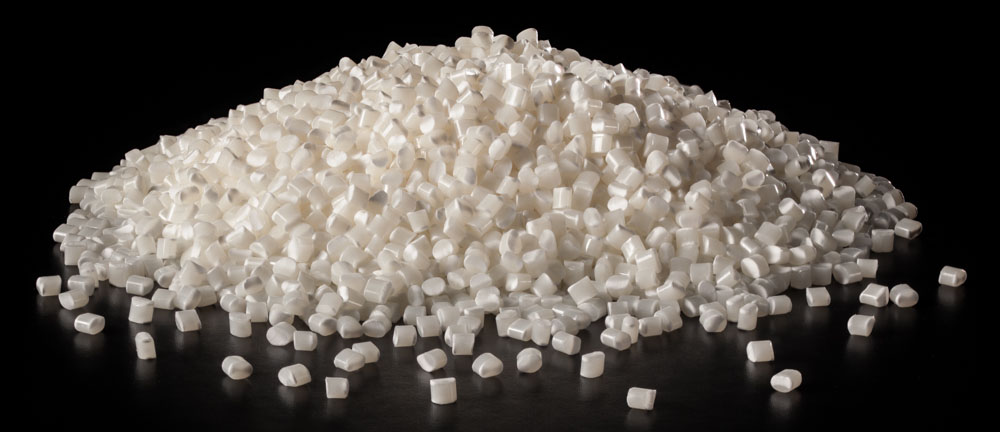
ABS plastic properties
ABS plastic is non-toxic and tasteless, with an ivory-colored translucent color.
The heat distortion temperature of ABS resin is 93 ~ 118 °C, and the product can be increased by about 10 °C after annealing treatment. ABS resin can be used in the temperature range of -40 ~ 100 °C.
ABS plastic has excellent mechanical properties and impact strength. ABS also has outstanding wear resistance, dimensional stability, and oil resistance; these features allow it to make bearings with medium loads and low speeds. ABS has greater creep resistance than PSF and PC, but less than PA and POM.
Plastic ABS has good electrical insulation and is almost unaffected by temperature, humidity, and frequency.
All of these properties make it one of the most popular plastic materials in the plastic molding industry.
In summary, the benefits of ABS plastic are as follows:
-
Good liquidity
-
Excellent impact resistance
-
Easy to form
-
Easy to color and spray
-
Good corrosion resistance
-
Matt effecting
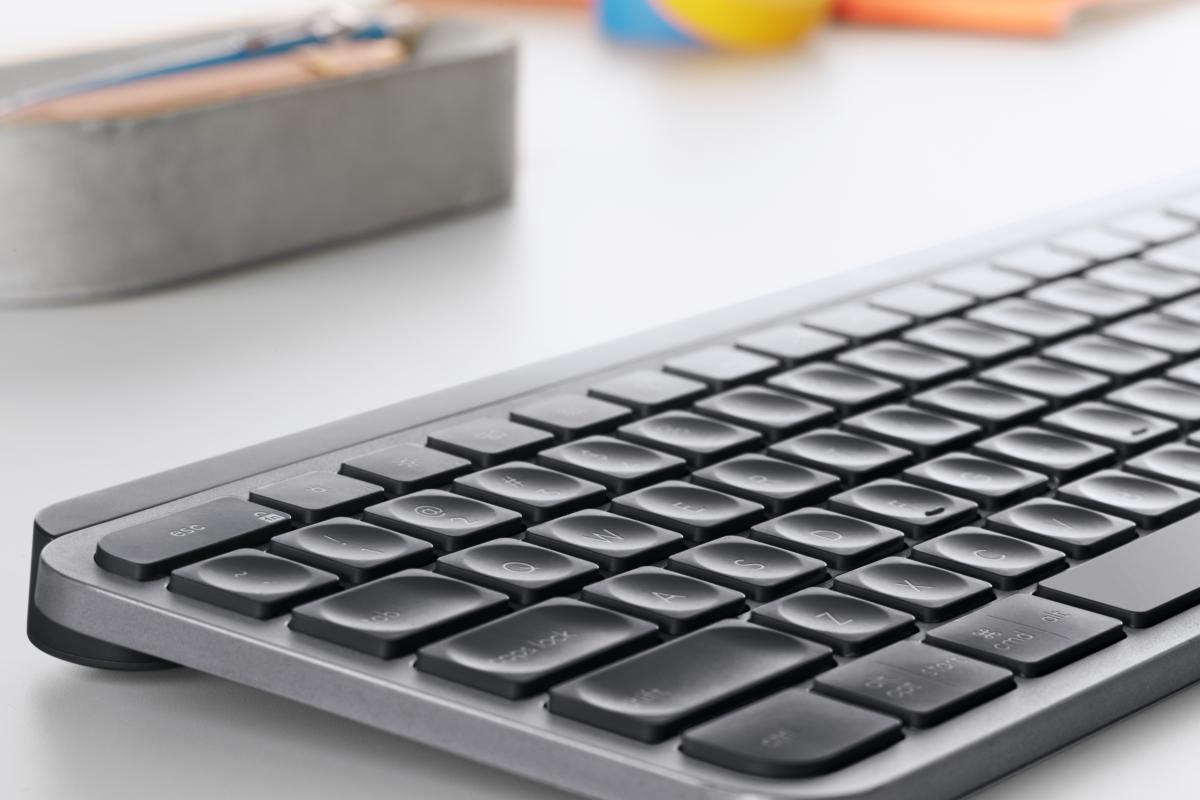
Different types of ABS material
A series of different types of ABS plastic can be produced by changing the formula of ABS or using different additives to meet the various requirements in the industry.
According to the impact strength: ultra-high impact type, high impact type, medium impact type, etc.
According to the ABS uses: general grade, heat-resistant grade, electroplating grade, flame retardant grade, transparent grade, antistatic, extruded sheet grade, pipe grade, and other varieties according to the characteristics of use and performance.
ABS plastic uses
The application fields of ABS resin are automobiles, electronic appliances, as well as good for 3D printing and rapid prototyping.
ABS plastic is used in the automotive field to make dashboards, body panels, interior trim panels, steering wheels, sound insulation panels, door locks, bumpers, ventilation pipes, and many other components.
In terms of electrical appliances, they are widely used, such as refrigerators, televisions, washing machines, air conditioners, computers, copiers, and so on.
In terms of building materials, ABS pipes, ABS sanitary ware, and ABS decorative boards are widely used in the building materials industry.
In addition, ABS is also widely used in packaging, furniture, children's toys, sports and entertainment products, machinery, and the instrument industry.
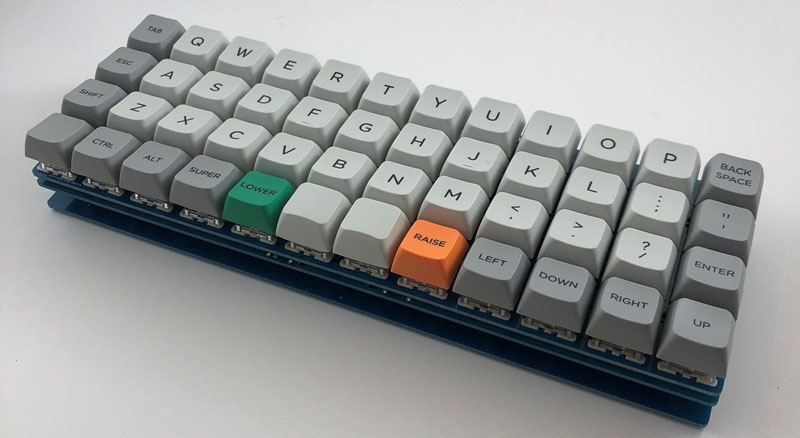
The manufacturing condition of ABS injection molding
ABS plastic drying: in winter: 75-80 °C, dry time: 2-3 ~ 3h, in summer: 80-90 °C, dry time: 4-8 hours.
ABS plastic has high hygroscopicity and sensitivity to moisture. Fully drying and preheating before processing can not only eliminate the fireworks like bubbles and silver thread on the surface of the part caused by moisture but also help the plastic reduce the color spots on the surface of the workpiece. ABS materials should control the moisture below 0.1%.
ABS melting point: 220 ~ 250 °C is good for the ABS melting temperature. Since the melting point temperature of ABS is high and it is sensitive to the process parameters, it is necessary to control the melting point temperature of the front end of the barrel and the nozzle part. Practice has proven that any small changes will be reflected in the product, such as melting marks and sink marks.
Injection molding pressure: 50-100 psi. The viscosity of ABS-melted parts is higher than that of polystyrene or modified polystyrene, so it needs a higher injection pressure. Of course, not all ABS parts require high pressure; small, thick parts need just lower injection pressures.
Injection molding speed: ABS material with a medium injection speed works better. When the injection speed is too fast, the plastic easily scorches or separates out vapors, resulting in defects such as welded joints and poor surface quality. However, when producing thin-walled and complex parts, it is necessary to ensure a sufficiently high injection speed; otherwise, it is difficult to fill.
Mold temperature: The mold temperature for ABS material is relatively high. Generally, about 75-85 °C. When producing parts of large size, the mold temperature requires 70-80 °C. When injecting larger, thin-walled parts, special heating of the mold needs to be considered.
Back pressure: The commonly used back pressure is 5 bar. The higher back pressure is needed for the coloring material to make the color mixing even.
There are lots of injection molding materials, and you should know well about the plastic properties of mechanics and chemistry so that you can use them to make perfect plastic products. Lushi ENGINEERING can give you more information about the injection molding manufacturing of ABS plastic. Please contact us if you need any help.