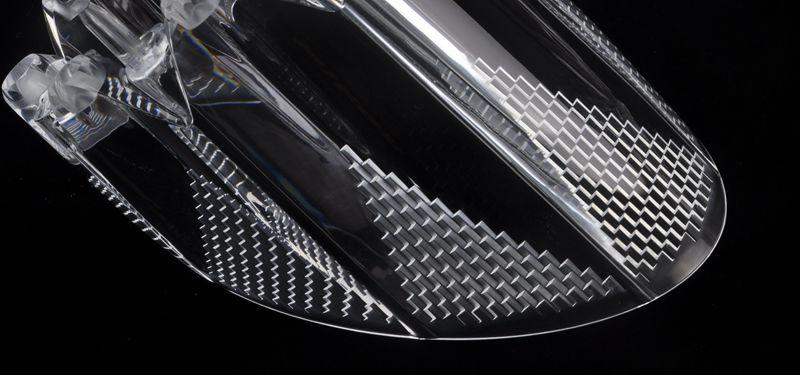
Such high-gloss plastic molds are often used in various fields such as medical technology or the automotive industry. Polishing the mold surface to a shiny or even high gloss has always been done by hand. This is very time consuming and expensive, which is very demanding on the skills and experience of the engineering. Since polishing is in most cases the last step of the process for tools and molds manufacturing, surface defects can have a significant impact on the plastic mold. There is still no systematic summary and explanation for the emergence and impact of such problems, so far there is no corresponding effective solution.
The finishing of molds can take up half of total production time, and this processing costs account for about 15% of manufacturing costs. On the one hand, in order to maintain the competitiveness of the market price, the small and medium-sized mold industry must meet shorter delivery times. On the other hand, the requirements for surface quality in mold manufacturing continue to increase. In the future, polishing can only be achieved by (partially) automated (manual engineers support up to 80% of activities) and related process processes.
How goes the polishing for injection tooling mold?
Polishing is not a separate manufacturing process and can only be combined with other processes such as sanding, grinding or polishing. If you look for a description in a textbook or on the internet, you will find different interpretations of polishing:
• “In the polishing process, abrasive particles, which in most liquid media finely dispersed, are carried out through the surface. Processing is achieved by superposition of chemical and mechanical action mechanisms.”
• “Polishing is the process of creating a smooth and shiny surface by rubbing or using chemistry to impart a significant specular reflection to the surface.”
• “Polishing means cleaning the object or surface with a soft cloth or a soft brush to make it glow.”
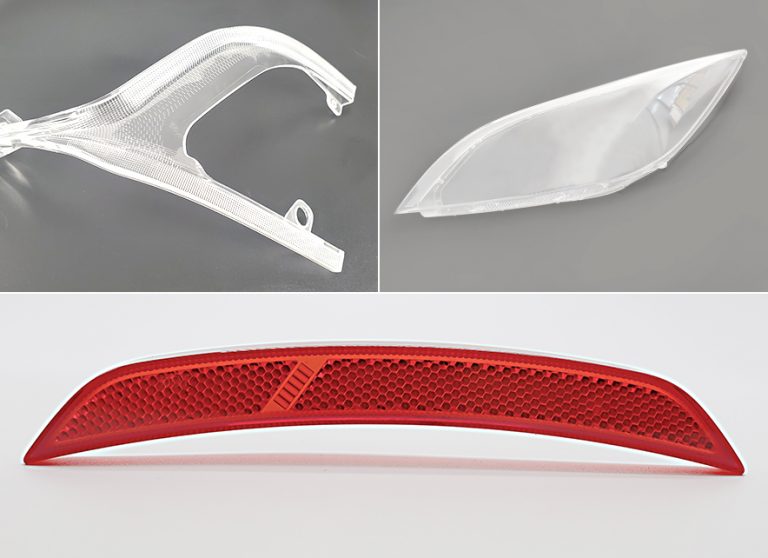
Future Prospect: Polishing Automation
• Develop a robust and repeatable process strategy.
• Prevent mistakes
• Reduce polishing time
• Support manual polishing machines (automation up to 80%)
The operator's sensory response is responsible for many manual polishing processes. Experience and process strategies are stored in his brain; power control and path planning are performed by the movement of the hand. Quality control is visual. In the automated polishing process, these complex processes that are intuitively performed by the manual polisher must be understood and known well by the machine. In various research projects, the process understanding of the manual polishing process as well as the automation of the finishing process and the identification of the machined surface will be promoted, which play a key role in polishing automation.
The goal of polishing automation research is to develop and identify automated polishing integrated systems for complex shapes of plastic molds, which greatly reduces manual, labor-intensive work and the high dependence of polishing results on operator experience.
For example, this can be achieved by a 6-axis articulated arm robot and a conventional manufacturing process (rotation and translational movement of the mold). On the robot, process strategies (tools, parameters, and web guidance) for automated processing are generated, including measurement systems for measuring surface quality. In addition, CAM modules can be used for off-line programming, optimization of polishing paths, and user-friendly use of robots. Based on the polishing strategy described above, the research on the polishing process of the demonstration components has been successfully completed.