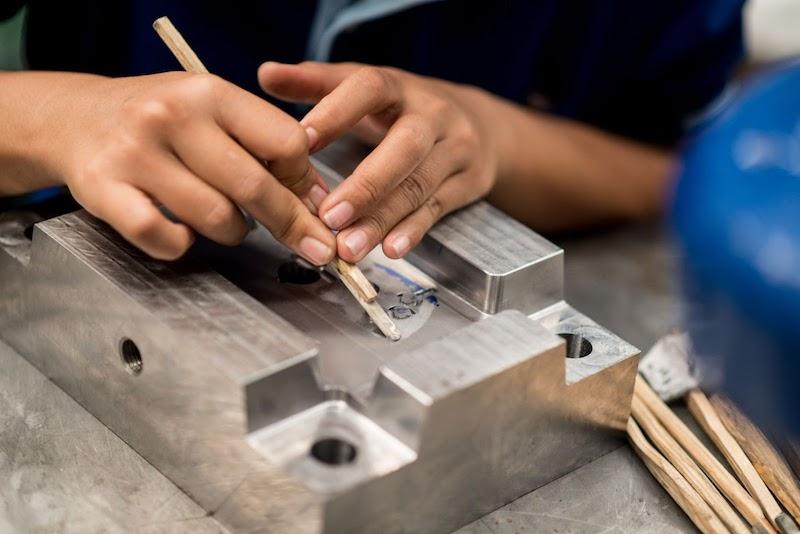
When it comes to injection-molded part manufacturing, the mold surface finish is an essential thing to consider if you want to deliver a quality and precise result. Before designing a mold surface, the most important factors to consider are the actual customer-specified dimensional tolerance as well as the material to be used for the mold creation.
To get the desired performance of plastic molded parts accurately, you need to consider some impacts of the mold surface finish, as below:
Injection mold surface finish affects material flow.
The injected materials are expected to get to every part of the cavity when injected into the mold, but if the surface finish is not adequately designed to allow this material to fill in the space, then it is evident that there would either be deformation in the molded parts or deficient filling pressure.
However, these could be prevented by first simulating the mold filling with the help of MoldFlow to know if the mold surface design will produce the desired output. In most cases, this is done by just entering in the preferred mold parameters, like dimensions, undercuts, thickness variations, and draft angles, in the MoldFlow software.
Substandard mold surface finish causes splay.
Splays are silver stripes marked on the surface of molded parts after the mold has been released. This happens as a result of tiny gas bubbles that are also pressured along with the elements as they enter the cavity. As these materials are heated before being shot into the mold, they produce wet substances that, when shot together into the mold, create these little bubbles around the surface of the injected material. In substandard surface finishing, these bubbles coagulate at the surface, creating silver streaks that damage the quality of the molded part.
However, there are varied ways to curb this situation, as it could significantly affect the appearance of the product and adversely affect the scheduled cost of production. Therefore, a proper mold surface finish needs an effective dryer to ensure that this moisture is appropriately expelled from the surface of the molded part before cooling. Besides, having a vent in the mold surface finish is the best way to release gas bubbles off the surface of the cavity of a mold and reduce the splays. This can also be solved by simulating the vent design.
Impact on the ejection process
Presently, most high-performance thermoplastics need a quality surface finish to mold efficiently. After molding, the ejection mold is supposed to release the clamping unit quickly. However, with faulty or substandard mold surface finishes, it will be difficult to puff the parts out. To prevent this from happening, primarily if it is used on materials that have a higher tendency to stick to the mold, and this is where the addition of textures is necessary to loosen the surface further, as it might occur in high-quality molds too.
How to achieve an excellent mold surface finish
Achieving an excellent mold surface finish, even with a high-gloss plastic parts, is important to get an accurate and precise molded part and is one factor that must be taken seriously in the molding process. Below are a few ways to attain an excellent mold surface finish.
Mechanical Polishing
This is a manual polishing process where welds and contaminants are smoothed off the mold surface through the process of grinding, buffing, and polishing. It is used to polish mold surfaces to a preferred level of roughness using materials like sandpaper or oil stone strips. Currently, this machining process will be performed by robotics to save time and expensive manpower.
High-quality manual grinding
High-quality manual grinding is used to achieve high precision in surface finishing. Manual grinders make use of stationary magnetic chucks under the grinding wheel, which rotates horizontally, and then the head is lower to the mold surface. As the head frictionally rubs on the mold in a back-and-forth movement, excess materials, weld paths, and spiral grind marks are rubbed off the surface, resulting in a highly efficient mold surface finish.
Nevertheless, there are many factors that influence the quality of the molded part. It is obvious that surface quality is one of the most important factors for excellent molding in an efficient injection molding process.