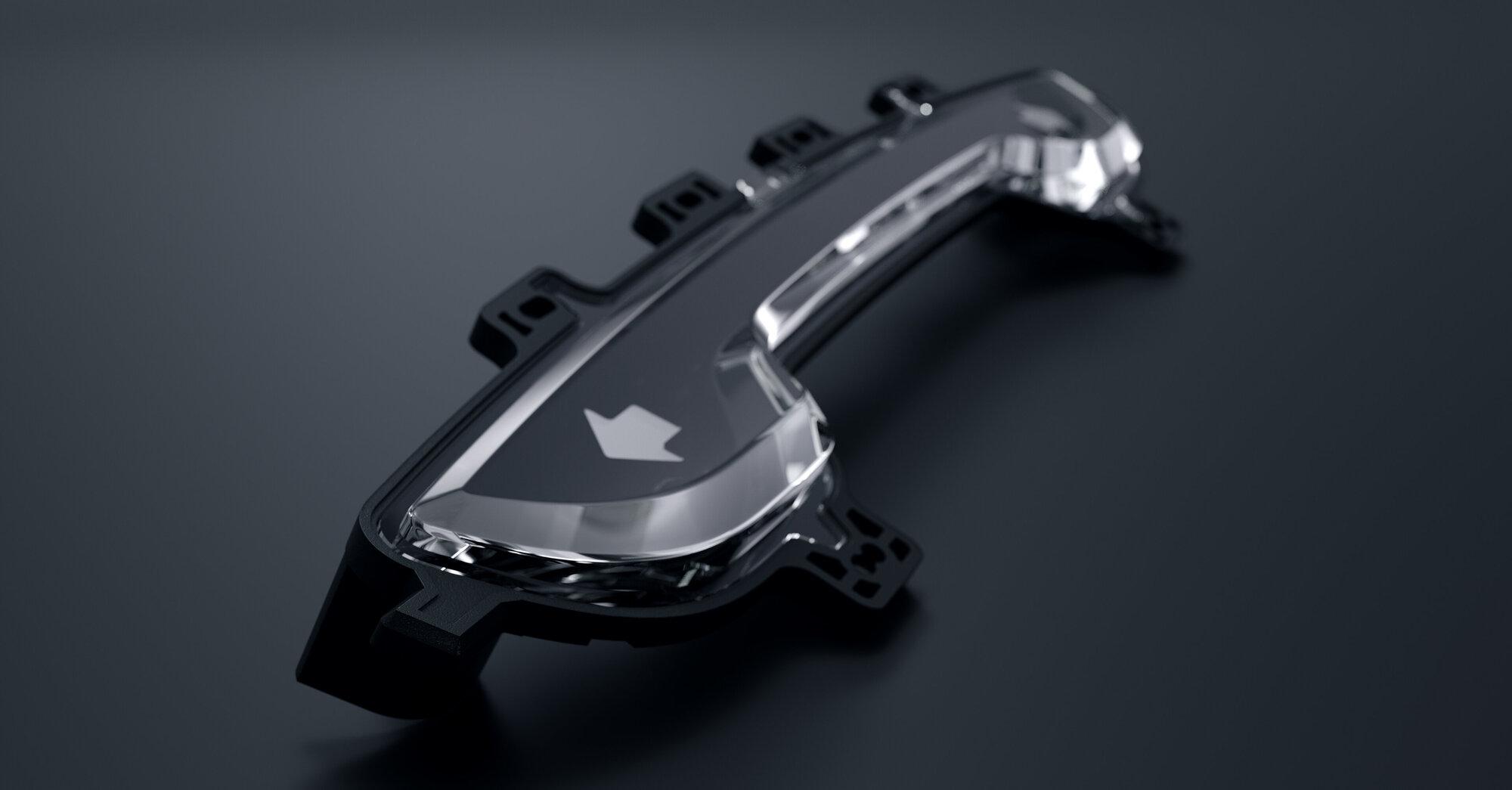
How can you correctly estimate the total costs of buying a plastic injection molding tool from China? What should we do to reduce the investment risk through the optimized project planning? The following guides are useful and practical for your procurement of injection tooling as well as plastic molded parts.
Why is the cost estimation of an injection tooling so complicated?
The cost of tooling involves many variables; it depends on the geometry of the molded parts and the shot time in the production. Tooling made of steel is more expensive than aluminum. The larger the cavity, the more expensive it will be. The real costs and delivery times can be determined via specific inquiries with some suppliers. The offers that follow are often sobering for the buyer due to the price differences of 50% and more, but it's normal, especially in China. Delivery times vary between a few weeks and many months, depending on the market situation. And the cheapest providers with the shortest delivery times are rarely Therefore, when we buy an injection mold, the price, quality, and risk should be measured. Here, LUSHI will give you some guides to show you how to optimize the total project cost to get the best quality.
What are the influence factors of the total cost of an injection molding tool?
A variety of factors can affect the total cost of purchase injection mold and plastic molded parts that you should pay for a tool, which consists of two areas:
Tooling costs: the prices offered for all items that are listed in the quotation for tooling.
Additional Costs: These costs will appear in the production process after the manufacturing of injection tooling, such as inefficient production, part defects, long cycle time, and mold wear, which could lead to immeasurable waste.
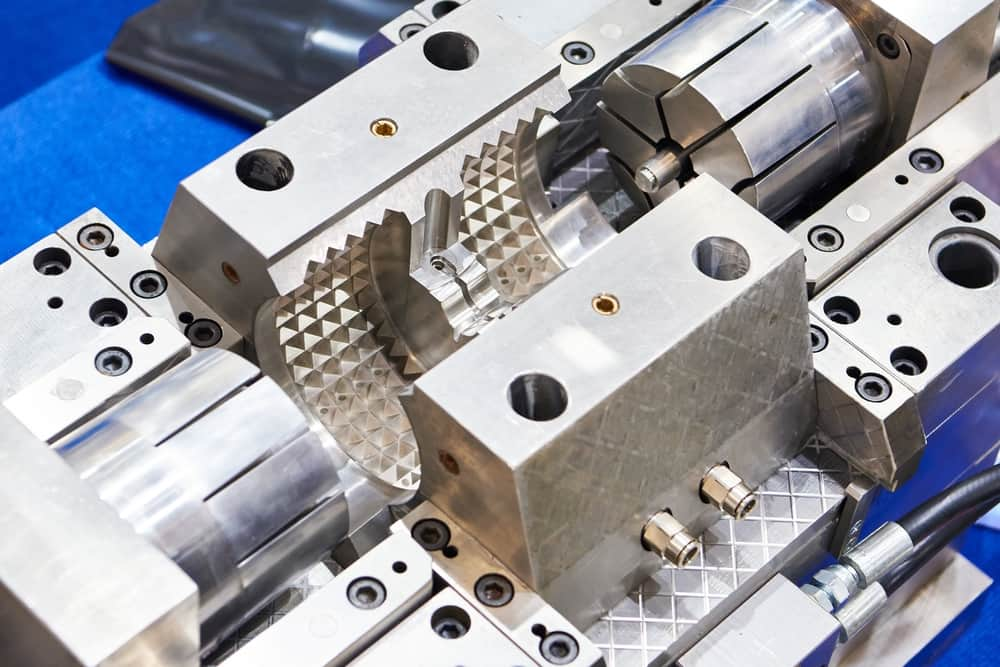
The whole cost of the tooling includes the following factors:
• Mold Design: Optimally constructed tooling eliminates many of the problems that could occur in future production and reduces cycle time, increasing production capacity and cutting down on overall costs. LUSHI has a professional engineering team that adapts the design perfectly to your needs, thus significantly reducing your procurement and maintenance costs and avoiding the huge additional costs in the subsequent production process.
• Parts design: The excellent plastic mold design can lower costs by reducing the complexity of the parts.
• Mold steel material: If the plastic injected parts are volatile or corrosive, it will produce higher temperatures and bigger pressure during the injection molding process for plastic parts. To meet these requirements, the mold steel requires outstanding material properties.
• Plastics material: Injection molding can be performed with a single material or a range of plastics, such as PP, ABS, PS, PE, PC, or TPU, depending on the specifications of the finished product. Buying mold materials might be expensive, depending on the material you choose. Material costs fluctuate over time. The model's design, the materials selected, and the volume of material required for the injection molding process all affect material prices.
• Precision tolerance: Precise injection-molded parts such as high-gloss parts require a high surface finish and additional manual grinding in post-production, which can considerably increase the manufacturing and maintenance costs of a mold.
• Annual Production Volume: In mass production of plastic parts, injection mold tooling requires sophisticated quality. By increasing the number of cavities, the production capacity can be increased; the disadvantage is the increase in the manufacturing cost of tools with multiple cavities.
• Part size: The larger the part size, the more material you need, resulting in higher material costs.
• Cycle time: In order to achieve a short cycle in plastic injection molding, the tool must cool the cavities quickly and homogeneously. A precise mold design improved the cooling time, which can also increase the cost.
• Cooling time: The cooling time and the uniformity of an injection mold have a strong impact on molding process efficiency. Uniform cooling throughout the cavity ensures the shortest cycle times in the process. Different cooling solutions will impact mold manufacturing significantly.
• Gate location: The gate location is a significant influence on molded parts. If the location of the gate on the mold side is impossible, that will need additional construction in the custom injection molding tool. In addition, using the hot runner system can significantly increase the price of the tooling, but it will also reduce the unit price of the molded part and tool complexity.
• Manufacturing costs: The manufacturing costs vary greatly among different suppliers, which is much more expensive with high-quality CNC centers than with general machines.
Overview of Injection Molding Costs
To help our customers understand the basic price components, the following chart illustrates the costs related to injection molding a hypothetical plastic product (such a small housing for an electronic device):
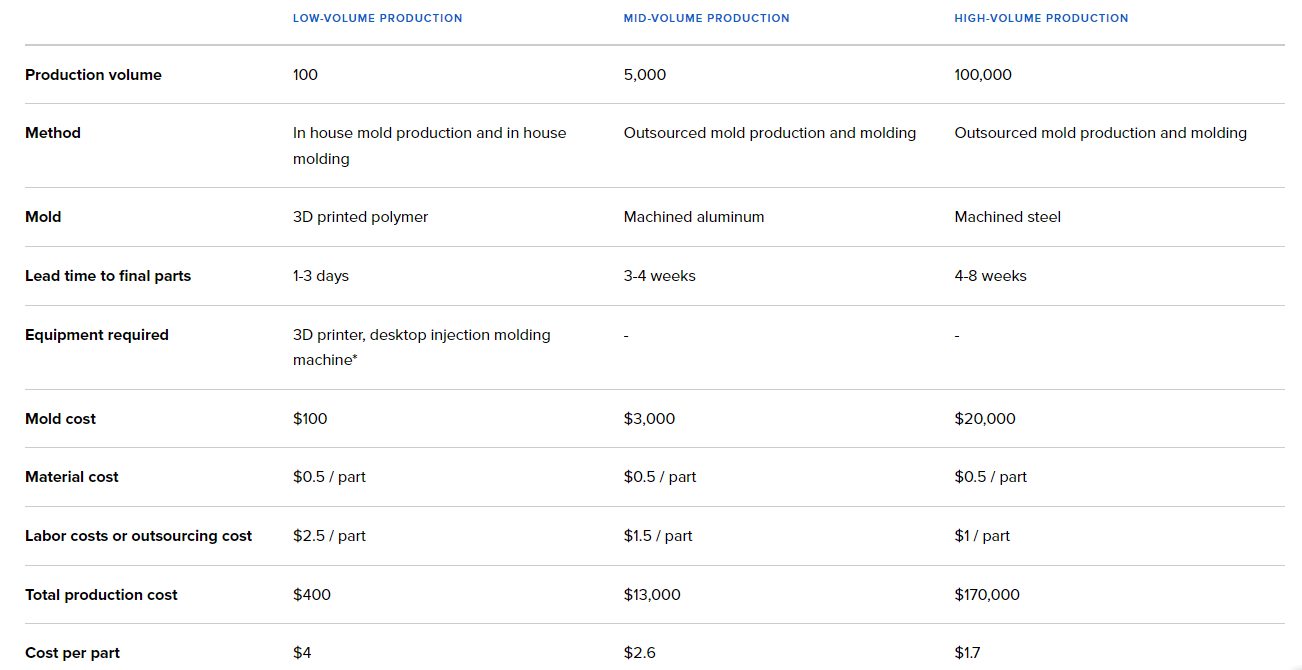
What is the additional cost of plastic injection molding in China?
✔ Choosing a supplier is not easy at all; it even costs a lot of time and money, including the cost of a personal visit to China.
✔ Due to the language barrier, misunderstandings can often occur, slowing down project progress.
✔ Most Chinese factories focus only on a specific area, such as tooling manufacturing without injection molding, just injection molding, or just part assembly. There are some big companies that contain all the production processes, but the delivery time is slower and the price is much higher than that of a normal manufacturer.
✔ Foreign companies that do not have QC in China sometimes need to personally fly to China to control the quality. This creates an additional cost burden.
✔ Tooling with a lower price has a risk of using tool steel with insufficient compositions or with inferior standard parts, resulting in an unexpected cost burden in the molding process.
How can LUSHI cut down the whole cost and reduce purchase risk?
Strategic Partnership: A long-term partnership between clients and LUSHI is the most critical factor in successful projects. We listen carefully to what customers really need and what we can do to win the goal. We often deal with customers to solve any difficulties together.
Optimization of mold design and molding process: Mold design and molding process optimization are the strengths of LUSHI. With our sufficient experience, our employees have gained more confidence to provide the best solution for our customers. Cost reduction, process optimization, and increasing productivity are our strategies for the plastic molding project. The quality risks that could occur in the production process are eliminated at the beginning of the project in order to reduce the cost burden for the customer in the later phase.
Making the most of your investment: LUSHI offers outlay cost planning (design, manufacturing, injection molding, assembly, and logistics costs, etc.) with economy and rationality for customers. We optimize the entire investment according to what needs to be spent and what can be spared. Overinvestment is wasting money, but underinvestment can hurt quality and cause additional costs in production, which is unpredictable.
One-Stop Service by LUSHI ENGINEERING: A complete project involves the following steps:
// Product design // Part design // Mold design // Purchase of materials // Tool manufacturing // Injection molding // Design of electronic circuits // Assembly of all individual parts // Logistic service
Different suppliers take these actions. The disadvantage is that it not only significantly prolongs the delivery time but also has a negative impact on production planning if there is a problem, which significantly increases the overall cost.
At LUSHI, our customers do not experience such problems with our one-stop service. In addition to the development and production of injection-molded parts, we also work with reliable electronics engineers, especially for home appliances, to find suitable solutions for the electronic circuits, thus significantly shortening the complete project. In addition, all steps will be under the control by LUSHI engineers on site.